Exploring the 2025 Market Trends for Carbon 3D Printers and Their Impact on Global Manufacturing
As we delve into the future of manufacturing, the emergence of remarkable technologies such as the Carbon 3D Printer is at the forefront of this transformation. These advanced printing solutions are not only revolutionizing the way products are conceived and produced, but they are also reshaping the entire landscape of global manufacturing. With their ability to create highly intricate designs rapidly and cost-effectively, Carbon 3D Printers are becoming indispensable tools for companies eager to enhance their production capabilities and innovate in an increasingly competitive market.
The year 2025 holds significant potential for the adoption of Carbon 3D Printing technology, with trends indicating a surge in both demand and application across various industries. This blog aims to explore these market trends and analyze how they will impact global manufacturing practices. By examining the advancements in materials, speed, and precision that Carbon 3D Printers offer, we can uncover the implications for manufacturers looking to stay ahead in a dynamic environment. As we navigate this transformative era in production, understanding these trends will be crucial for identifying new opportunities and challenges that lie ahead.
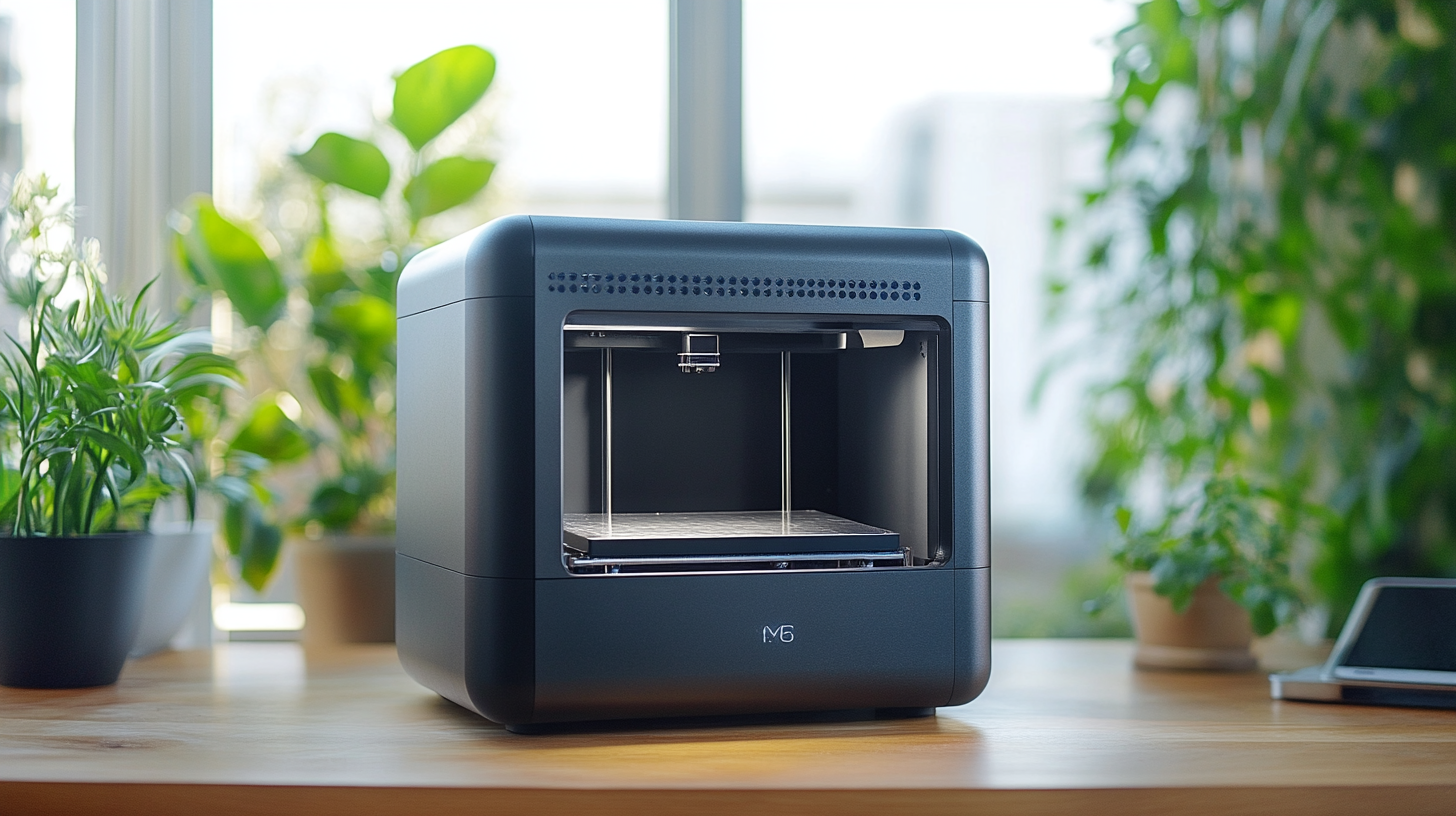
Evolving Technologies: Key Innovations in Carbon 3D Printing for 2025
In 2025, the landscape of Carbon 3D printing is poised for transformative growth, driven by key technological innovations and the increasing demand for customized solutions across various industries. One of the most noteworthy advancements is the integration of advanced lightweight materials, such as carbon composites, which significantly enhance the performance and efficiency of 3D printed products. According to recent industry reports, the Carbon 3D printing market is expected to reach a valuation of approximately $5 billion by 2025, rising at a compound annual growth rate (CAGR) of over 25%. This surge highlights the critical role that Carbon 3D printing will play in global manufacturing. A significant trend identified in executive surveys is the rising adoption of dental 3D printing technologies. Customizable dental devices created through Carbon 3D printing are revolutionizing how dental professionals approach patient care. The capability to produce tailored aligners and implants on-demand not only improves patient outcomes but also reduces the time and costs associated with traditional manufacturing processes. Experts predict that the dental 3D printing market will grow substantially, driven by these innovations and an expanding user base. Moreover, events like TCT Asia 2025 will showcase groundbreaking developments in Carbon 3D printing, offering industry professionals a platform to exchange ideas and explore collaborations. As new technologies emerge, businesses can leverage these advancements to enhance their manufacturing capabilities, ultimately driving efficiency and productivity in a competitive global landscape. The evolution of Carbon 3D printing is not just about technology; it's about reshaping the way industries think about production and customization in the years to come.
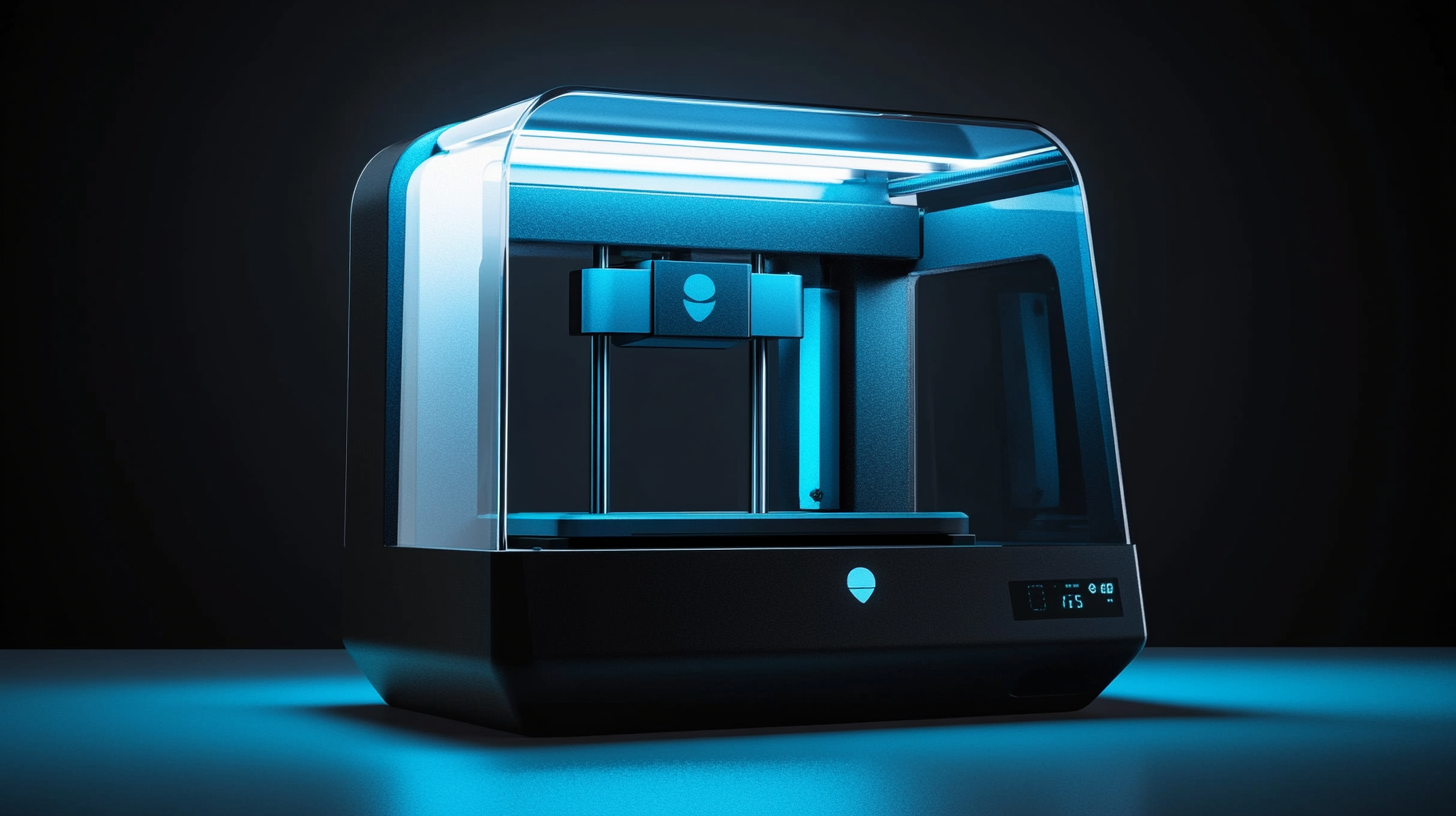
Sustainability and Efficiency: The Role of Carbon 3D Printers in Eco-Friendly Manufacturing
As the world grapples with the pressing need for sustainable manufacturing solutions, Carbon 3D printers emerge as a key player in the eco-friendly technology landscape. With their advanced digital light synthesis technology, these printers not only deliver high-quality, precise parts but do so in a manner that significantly reduces waste and energy consumption. Traditional manufacturing processes often rely on subtractive methods that generate excess material and require substantial energy input. In contrast, Carbon 3D printing utilizes a layer-by-layer approach that optimizes material usage and minimizes environmental impact.
Moreover, the efficiency provided by Carbon 3D printers can drastically enhance production timelines. In industries where rapid prototyping and quick turnarounds are essential, the ability to produce complex geometries with less material and energy consumption stands out. Businesses can see shorter lead times and increased flexibility in design, all while adhering to sustainability principles. This seamless integration of efficiency and eco-consciousness positions Carbon 3D printers not just as tools for production, but as essential components of a new paradigm in sustainable manufacturing.
The implications of adopting Carbon 3D technology extend beyond mere cost savings or enhanced productivity; they redefine corporate responsibility in manufacturing. Companies that choose to implement these innovative solutions are not just improving their bottom lines—they are making a commitment to environmental stewardship. In a world increasingly driven by consumer demand for sustainable products, the role of Carbon 3D printers in shaping a greener manufacturing landscape is not only timely but vital for future global industry standards.
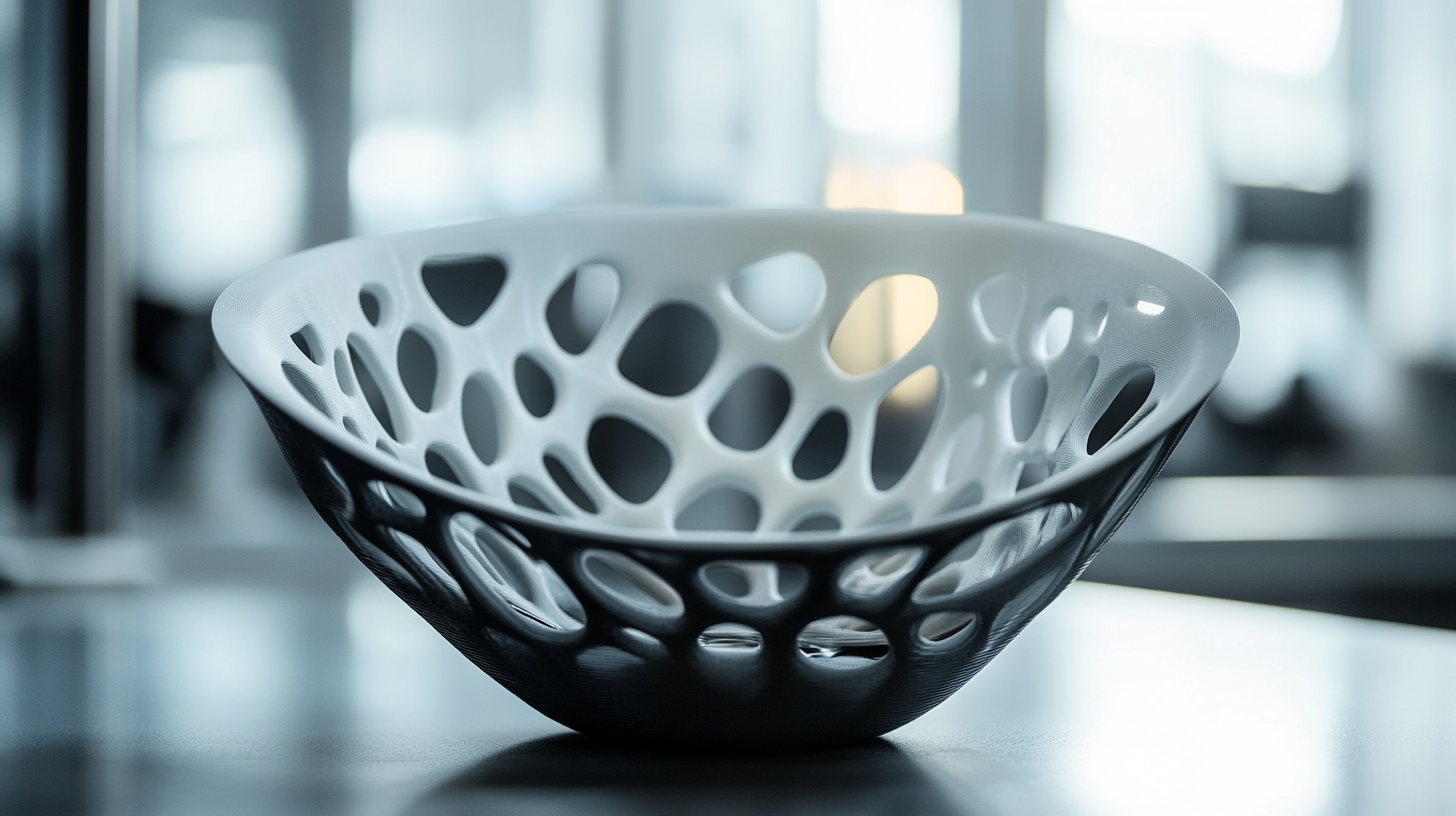
Market Dynamics: How Carbon 3D Printers Are Shaping Global Supply Chains
As the global manufacturing landscape evolves, the integration of Carbon 3D printers is emerging as a pivotal force in shaping supply chains. By 2025, the adaptability and efficiency of these printers are set to streamline production processes across various sectors. For instance, a recent survey highlights that approximately 70% of industry leaders anticipate significant improvements in operational efficiencies and cost reductions due to the deployment of advanced additive manufacturing technologies like Carbon 3D printing.
The trend towards digital manufacturing is increasingly evident in the aerospace and automotive industries, where the demand for lightweight materials and optimized components is skyrocketing. As reported, the 3D printing market is projected to expand rapidly, particularly with innovations enhancing sustainability practices. An executive survey indicates that 60% of leaders in these sectors are investing in 3D printing technologies as they seek to reduce waste and improve their supply chain resilience in the face of fluctuating raw material availability.
Furthermore, the convergence of smart supply chain practices with 3D printing technology is estimated to drive the global smart supply chain market to USD 62.8 billion by 2032. This integration not only revolutionizes how products are developed and delivered but also mitigates risks associated with traditional manufacturing approaches. By leveraging real-time data and insights from Carbon 3D printers, manufacturers can respond more effectively to consumer demands, thus enhancing their competitive edge in the market. As we look toward 2025, these dynamics underscore a transformative shift in how industries operate and interact within the global supply chain ecosystem.
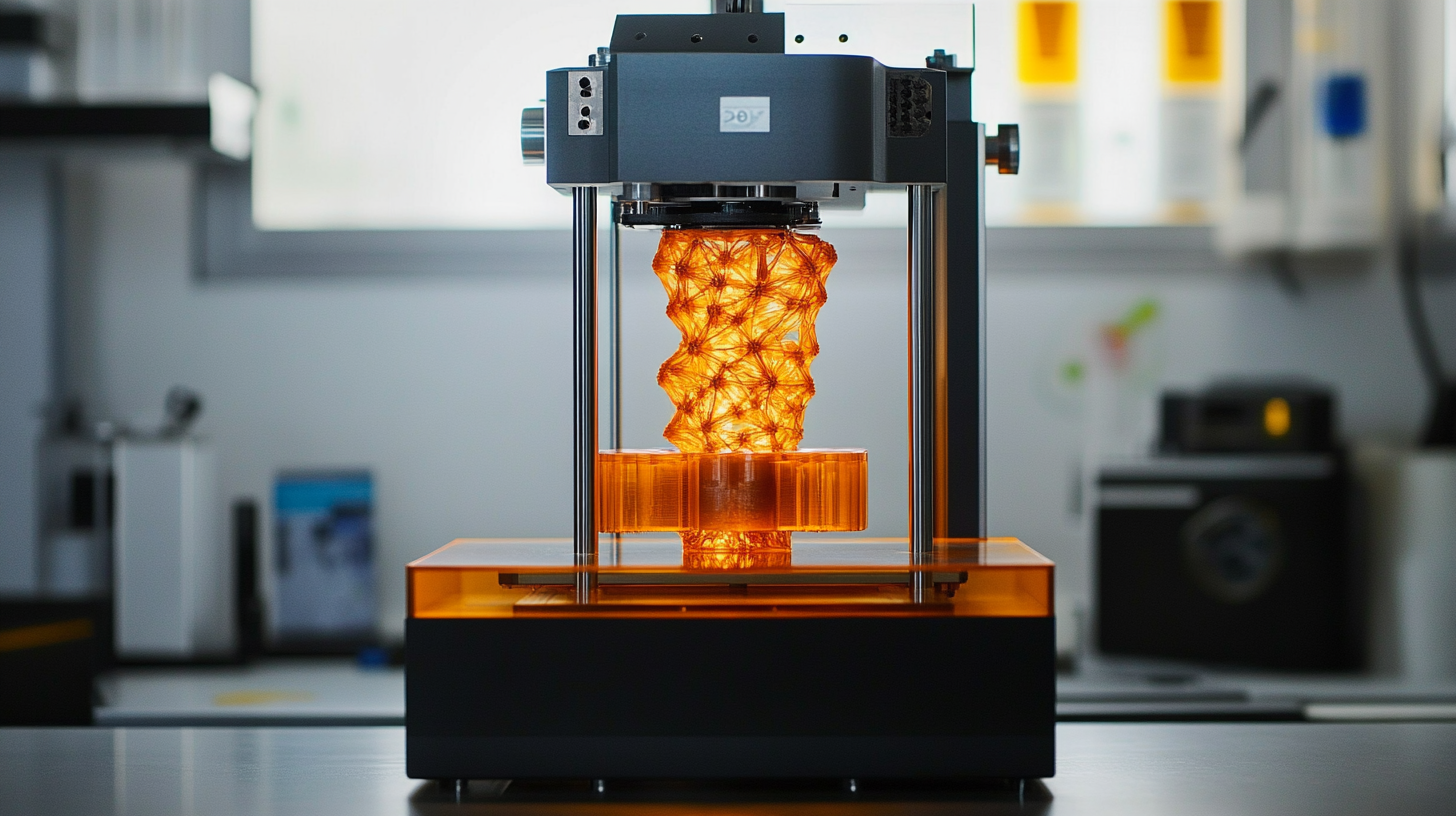
Challenges Ahead: Addressing Barriers to Adoption of Carbon 3D Printing Technology
The adoption of Carbon 3D printing technology is at a pivotal juncture, with numerous challenges hindering its widespread implementation in global manufacturing. According to a recent report by SmarTech Analysis, the market for Carbon 3D printers is projected to reach $1.5 billion by 2025. However, the transition from traditional manufacturing methods to advanced additive manufacturing systems is fraught with challenges that could impede this growth.
One primary barrier is the high cost associated with Carbon 3D printers and their materials. The initial investment for companies can be substantial, with a single printer priced between $25,000 and $50,000. Additionally, the proprietary materials required for Carbon printing can further inflate operational costs, making it difficult for small and medium-sized enterprises to justify the switch. A survey from the National Association of Manufacturers indicates that nearly 70% of manufacturing companies cite cost as a significant barrier to adopting new technologies.
Furthermore, there is a considerable skills gap in the workforce regarding new additive manufacturing techniques. According to a report from Deloitte, almost 2.4 million manufacturing jobs could go unfilled by 2028 due to a shortage of skilled labor. As Carbon 3D printing relies on advanced design and operational knowledge, this gap presents a significant challenge for companies looking to innovate and remain competitive in the evolving market landscape. Without targeted workforce development initiatives, the potential of Carbon 3D printing may remain untapped, limiting advancements in production capabilities and efficiency.
Future Opportunities: Emerging Applications and Industries for Carbon 3D Printing in 2025
As we approach 2025, the implications of carbon 3D printing are poised to transform various industries, with new applications emerging that highlight its versatility and sustainability. With researchers advocating for a sustainable and circular additive manufacturing ecosystem, carbon 3D printers are set to play a crucial role in reducing waste and advancing eco-friendly production methods. This shift is not just a trend but a necessary evolution in response to global demands for more sustainable manufacturing practices.
Industries such as aerospace, electronics, and healthcare are expected to lead the charge in adopting carbon 3D printing technologies. The aerospace sector is particularly noteworthy, as it embraces innovations like artificial intelligence and enhanced materials to improve efficiency and reduce costs. The demand for lightweight, high-strength components can be significantly met through carbon 3D printing, paving the way for greener aviation solutions. In the electronics realm, the integration of carbon nanotubes into 3D printing processes promises advancements in conductive materials, fostering new product development.
Furthermore, with the expected growth of the overall 3D printing market—forecasted to reach $29.4 billion by 2029—businesses are increasingly exploring opportunities to leverage these technologies for custom solutions. The convergence of AI-driven tools and carbon printing means that bespoke designs can be realized faster and more efficiently than ever before, propelling industries toward a future where innovation and sustainability go hand in hand.