Maximizing Efficiency in 3D Printing with Advanced Material Selection Techniques
In the rapidly evolving world of manufacturing, 3D printing has emerged as a transformative technology that enables the creation of complex structures with unprecedented levels of customization. However, the efficiency of 3D printing processes is heavily influenced by the selection of appropriate materials. As industries continue to adopt this innovative method, understanding how to maximize efficiency through advanced 3D printing materials becomes paramount. The right materials not only enhance the mechanical properties of printed objects but also can significantly reduce production time and costs, leading to a more sustainable manufacturing workflow.
In this blog, we will explore various advanced material selection techniques that can optimize the performance of 3D printing. By investigating the impact of different materials on the speed, quality, and cost of production, we aim to provide insights that can help businesses leverage 3D printing to its fullest potential. Whether you are a seasoned manufacturer or just starting in the world of 3D printing, this discussion on material selection will equip you with the knowledge to make informed decisions and improve your operational efficiency.
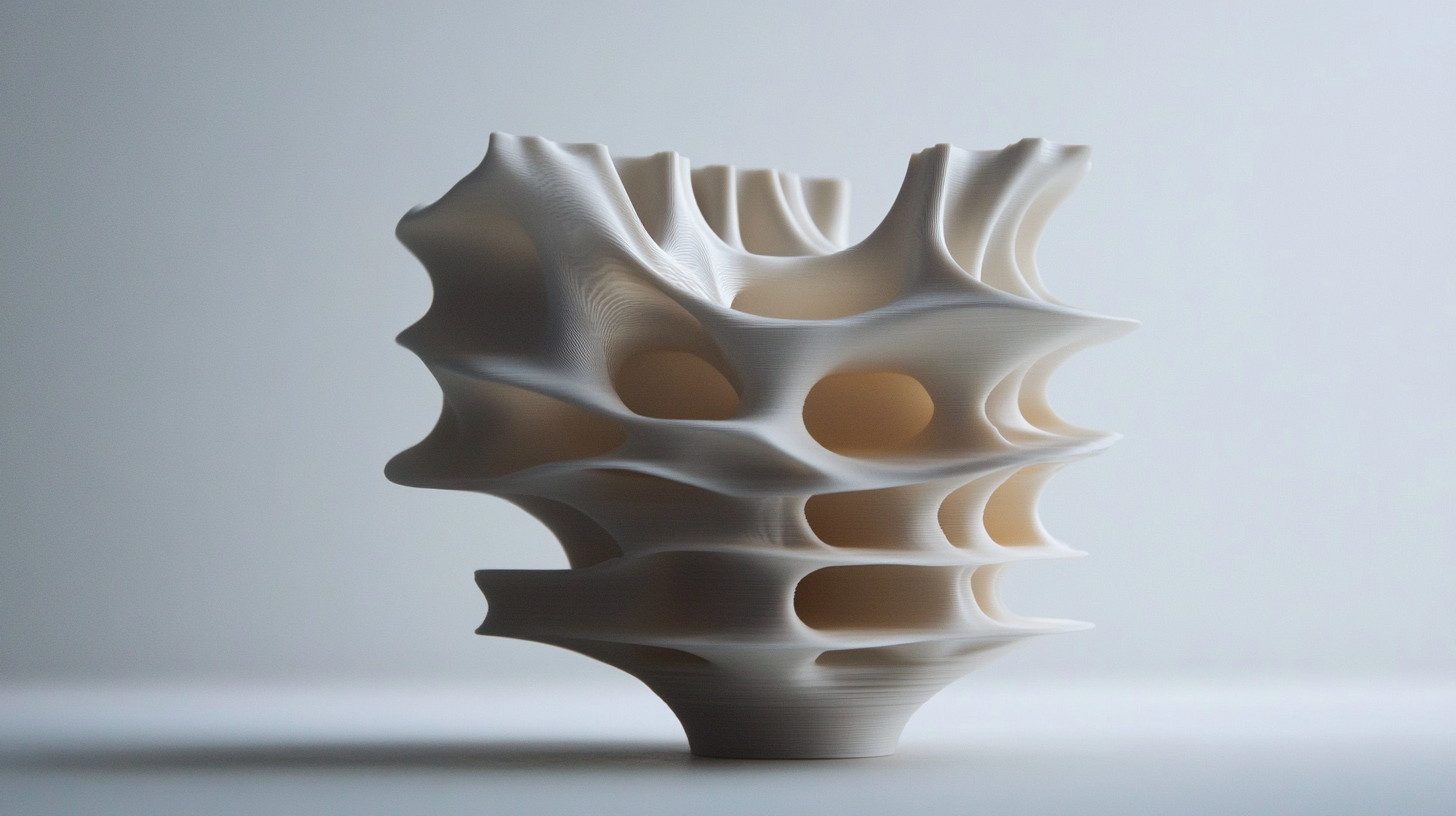
Understanding the Importance of Material Selection in 3D Printing Efficiency
Material selection is a pivotal factor in achieving high efficiency in 3D printing. The type of material chosen can significantly influence the printing process, the final product's properties, and overall production timelines. Each material has its unique characteristics, such as strength, flexibility, and thermal resistance, which can either enhance or hinder the printing process. Understanding these properties allows designers and engineers to select materials that not only suit the specific requirements of a project but also optimize the printing workflow. Advanced material selection techniques enable users to evaluate their options meticulously, considering factors such as cost, availability, and environmental impact. For instance, the use of composite materials might provide superior mechanical properties while still being lightweight, thus improving print speed and reducing material waste. Additionally, innovations like bio-based materials or recycled filaments are becoming increasingly popular, offering sustainable alternatives without sacrificing quality. By leveraging these advanced techniques, manufacturers can not only enhance the performance of their 3D printed items but also contribute to a more sustainable manufacturing process. Ultimately, the importance of material selection cannot be overstated. It serves as the foundation upon which the efficiency of the entire 3D printing process rests. By prioritizing the right materials, companies can achieve faster turnaround times, lower costs, and superior product performance, making material selection a crucial part of any 3D printing strategy.
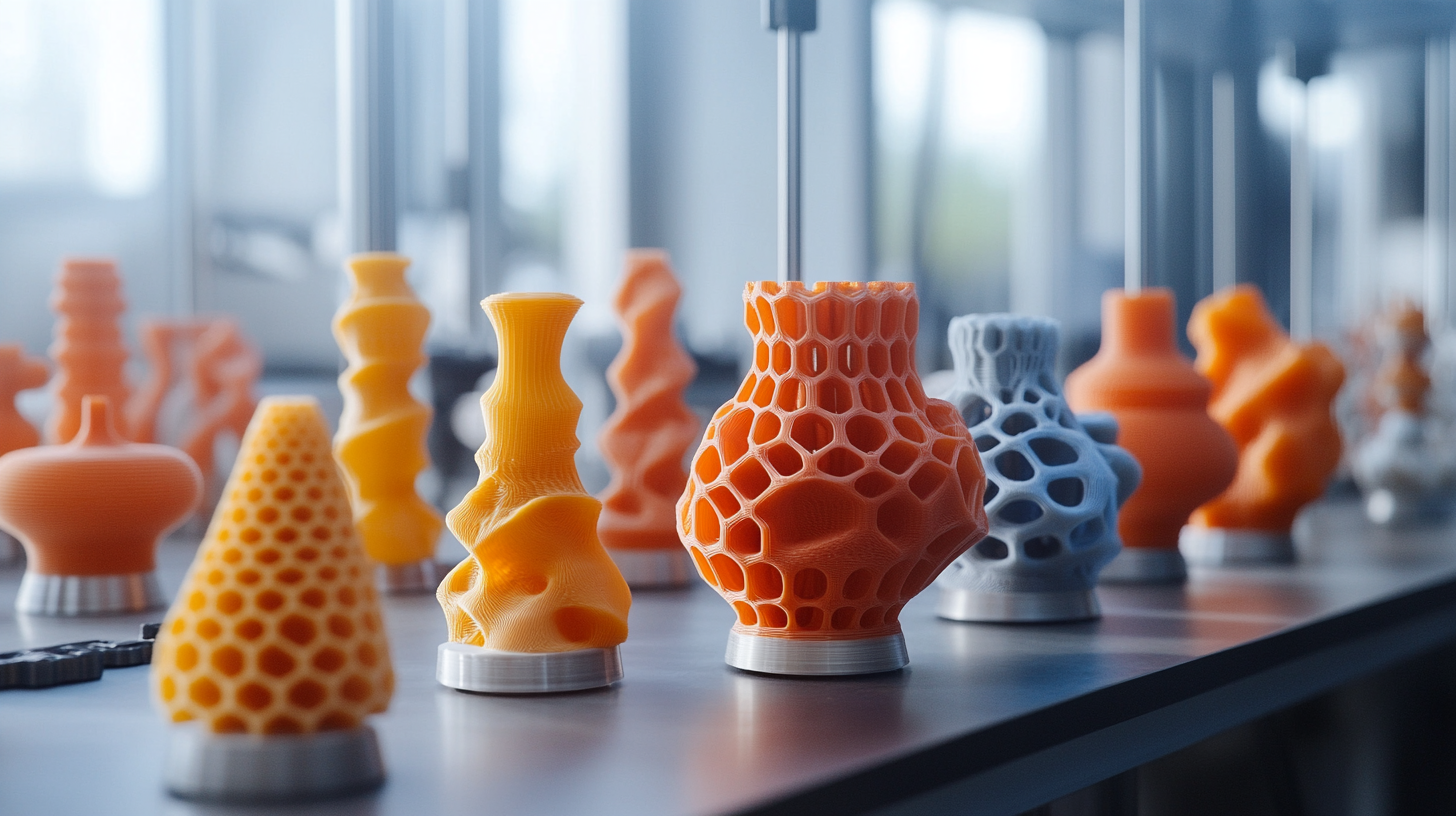
Key Factors Influencing Material Performance in 3D Printing Applications
The selection of materials plays a critical role in maximizing efficiency in 3D printing applications. Recent advancements in optimizing the mechanical performance of 3D-printed polymer composites highlight the importance of material choice and processing techniques. By understanding microstructural elements, researchers are now able to enhance properties like tensile strength and impact resistance. For instance, studies have shown that careful manipulation of processing parameters can significantly influence the mechanical behavior of materials, resulting in improved performance in demanding applications.
Moreover, the exploration of metal 3D printing has unveiled how different printing orientations and scanning times can affect the mechanical properties of materials like 17-4 PH stainless steel. These insights emphasize the need for diligent material selection and production strategies to ensure optimal performance. As researchers like Diane Collard work to make energetic materials safer and more effective through 3D printing, it becomes evident that the interplay between material properties and application requirements is crucial for achieving desired outcomes.
Additionally, developments in 3D printing technology are paving the way for innovative solutions in areas such as water treatment and eco-friendly construction. By integrating advanced materials with innovative design capabilities, 3D printing is redefining industry standards. This evolution not only enhances the functionality of printed components but also promotes sustainability in manufacturing practices. As the industry continues to advance, attention to material selection will remain a key factor in driving efficiency and performance in 3D printing applications.
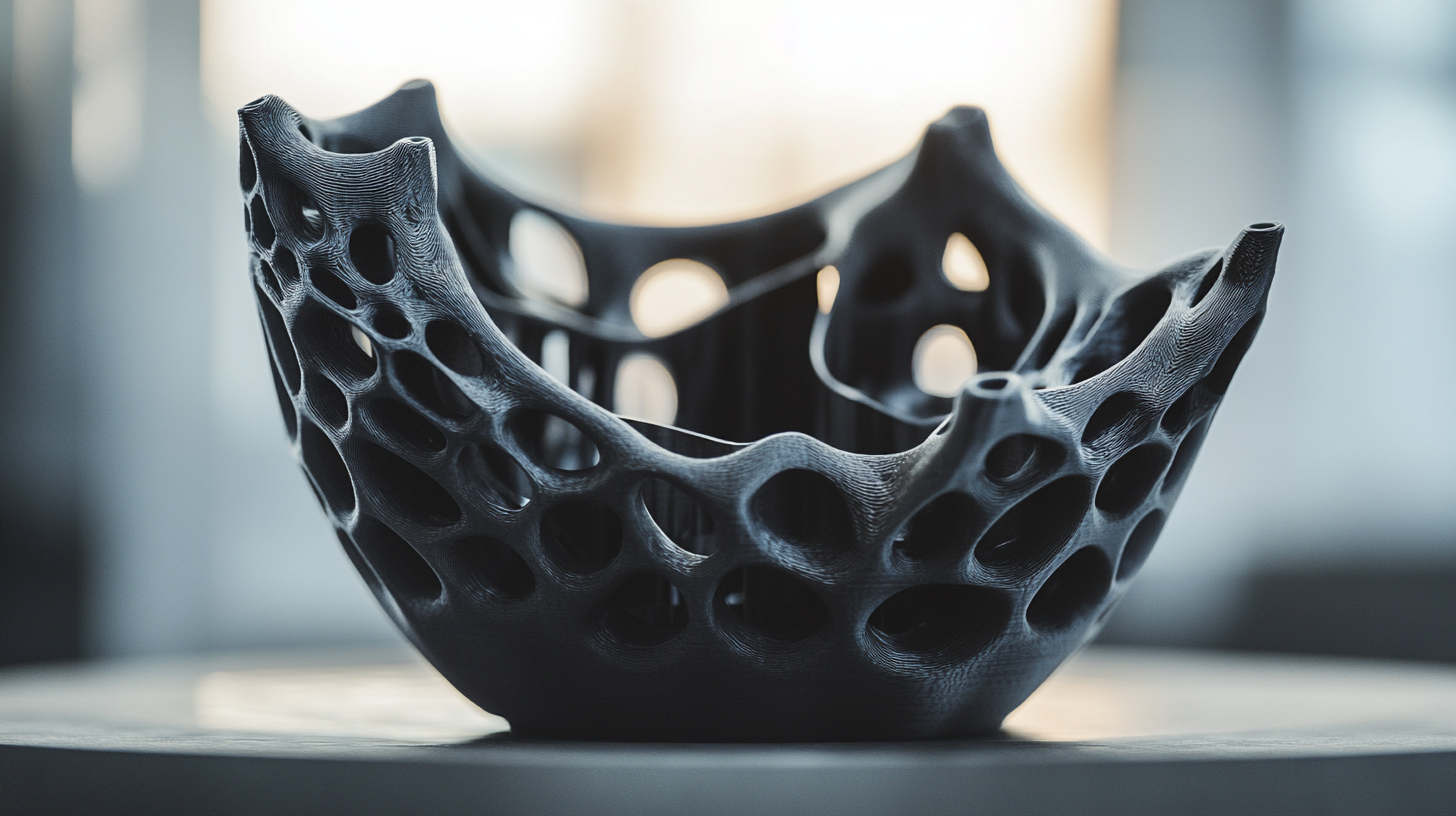
Innovative Techniques for Advanced Material Selection in 3D Printing
In the realm of 3D printing, the selection of materials plays a pivotal role in defining the quality and application of the final product. Innovative techniques for advanced material selection have emerged, enabling designers and engineers to optimize performance while meeting specific project requirements. By integrating advanced computational models and simulation tools, practitioners can now predict how different materials will behave under various conditions, allowing for more informed choices that enhance the overall efficiency of the printing process.
One prominent technique involves the utilization of material databases, which compile extensive properties and performance metrics of a wide range of substances. These databases, often powered by machine learning algorithms, facilitate quick comparisons between materials, helping users to identify the best candidates for their specific needs. Moreover, advancements in design software that include these databases can streamline the workflow, reducing the time spent on material selection and significantly speeding up the development cycle.
Furthermore, incorporating hybrid approaches that combine additive manufacturing with traditional techniques offers new possibilities in material selection. For instance, designers can experiment with composite materials that blend the strengths of multiple substances, leading to enhanced mechanical properties and reduced weight. This synergy not only maximizes efficiency but also expands the horizons of what can be achieved with 3D printing, bringing forth new applications in sectors ranging from aerospace to medical devices. By embracing these innovative techniques, the future of 3D printing stands to revolutionize how we create and utilize materials.
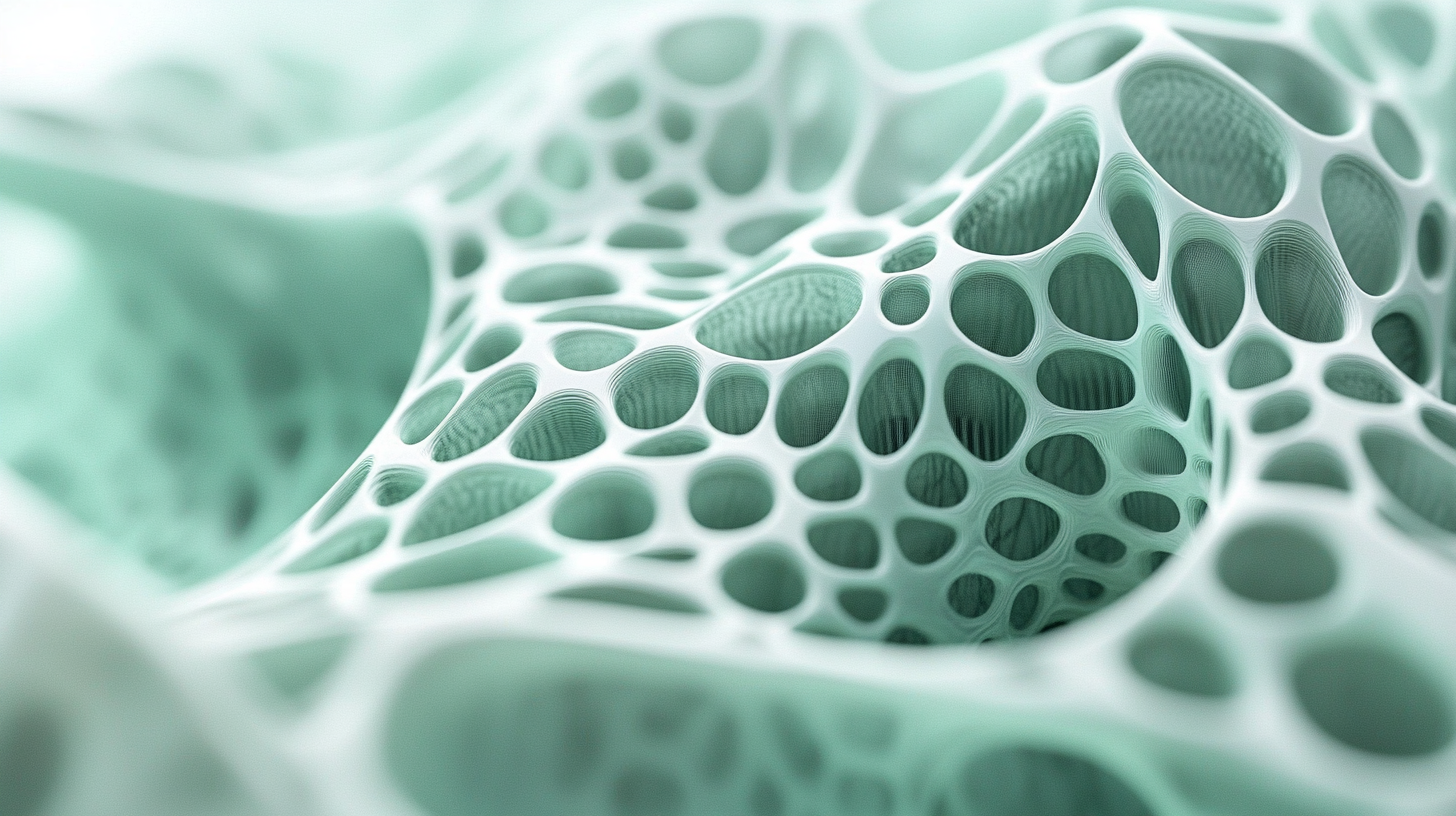
Case Studies: Impact of Material Choices on 3D Printing Outcomes
In the realm of 3D printing, the selection of materials plays a pivotal role in determining the efficacy and quality of the final product. Recent case studies have illuminated how specific material choices can significantly influence printing outcomes across various applications. For instance, a case involving the production of lightweight aerospace components showcased that using carbon fiber-reinforced polyamide enhanced both the mechanical strength and thermal stability of the pieces. This allowed for reduced overall weight without compromising performance, illustrating that advanced material selection can lead to innovative breakthroughs in industries where every gram counts.
Another compelling case involves the medical sector, where the use of biocompatible materials for prosthetics has revolutionized patient care. By employing flexible thermoplastics, developers achieved a comfort level unprecedented in traditional prosthetic design. These materials not only adapted better to the body’s movements but also improved the overall fit for individual patients. This shows that the right material choice can directly enhance user experience and functionality, demonstrating the transformative power of advanced material strategies in 3D printing.
Additionally, in the automotive industry, experiments with thermoplastic elastomers revealed significant advancements in part durability and elasticity. A notable case study showed that components produced with these materials exhibited greater resistance to wear and tear while maintaining superior flexibility compared to conventional materials. This finding indicates that informed material selection can streamline production processes and yield longer-lasting products, ultimately benefiting manufacturers and consumers alike.
Future Trends in Material Science for Enhanced 3D Printing Efficiency
The landscape of material science is rapidly evolving, leading to groundbreaking advancements in 3D printing efficiency. One of the most exciting trends is the development of multifunctional materials that can serve multiple purposes. For instance, self-healing polymers and responsive materials can adapt to environmental changes, reducing the need for post-processing and increasing the durability of printed objects. This not only accelerates production timelines but also enhances the overall reliability of 3D printed components, making them suitable for critical applications in industries such as aerospace and healthcare.
Another trend reshaping the efficiency of 3D printing is the integration of nanomaterials into traditional substrates. By incorporating nanoparticles, researchers are significantly improving the mechanical properties and thermal stability of printed objects. This innovation facilitates the creation of lightweight yet robust structures, enabling designers to push the boundaries of creativity while maintaining functionality. The ability to tailor materials at the nanoscale opens up endless possibilities for custom designs and highly specialized applications.
Moreover, sustainable materials are gaining traction as more manufacturers seek eco-friendly alternatives. Innovations in bio-based filaments not only reduce environmental impact but also enhance the performance of 3D prints. As these materials continue to evolve, we can expect a shift towards a circular economy where waste is minimized, and resources are recycled efficiently. This trend not only supports sustainability but also encourages the development of new ecosystems around 3D printing technologies.